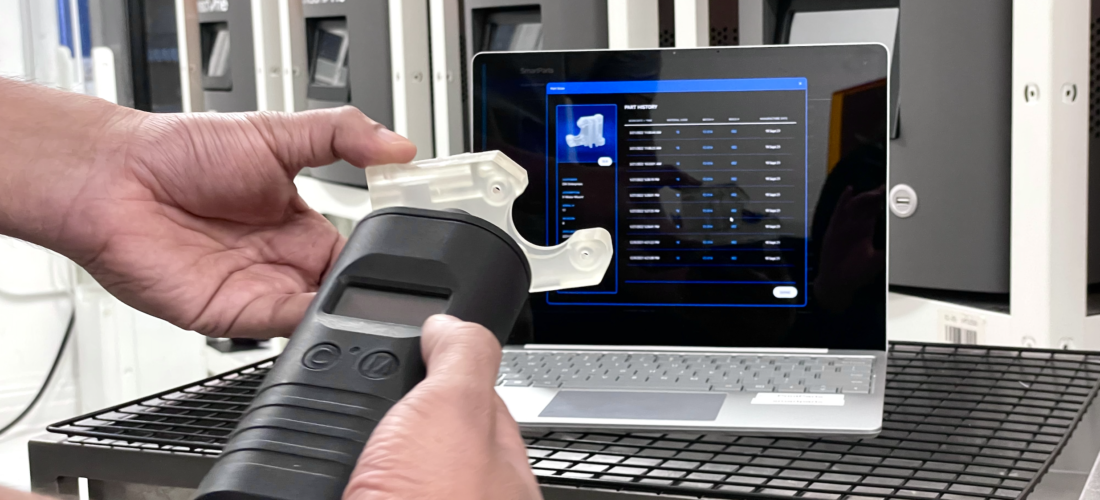
SmartParts: Traceability in 3D Printing at the Particle Level – 3DPrint.com
- On March 21, 2022
The 3D printing industry is currently maturing, with many developments underway that will better enable its use in end part manufacturing at scale. Among these developments are improved post-processing, greater automation, and improved quality control, all of which are discussed in the “Automation, Additive Manufacturing and the Factory of the Future” report from SmarTech Analysis.
Not all of the approaches to these areas is as straightforward as one might think. For instance, much of the traceability necessary for improved quality control is being tackled through the use of new software tools, such as manufacturing execution systems (MES). However, there’s one method that is quite unique in its method for tackling traceability. It’s called SmartParts and, though it relies on software to track parts, it does so at the material level. That is, it is the material itself that enables the tracking. To learn more, we spoke to Cody Burke, the co-founder and chief operating officer of PrintParts, the firm behind SmartParts.
PrintParts itself began as and continues to be a boutique service bureau located in Manhattan. There, co-founder Robert Haleluk set up shop to apply his expertise in the injection molding industry to the world of additive manufacturing (AM). Burke, in turn, came from MakerBot before it was acquired by Stratasys, where he spent seven years as director of investor relations.
The business has a fleet of over 50 printers, including about 30 Markforged systems, some ETEC machines, and five Fuse 1 selective laser sintering systems from Formlabs, making it the largest user of Fuse 1 equipment so far. With that setup, the company acted as the prime contractor from New York City for COVID response, producing over 1.5 million 3D printed nasal swabs. It was when Burke joined that they “re-founded” PrintParts with the goal of introducing SmartParts to market.
“Probably around 70% of our business is production runs. That’s what we really focus on, as opposed to the prototyping side of things. And that’s really informed the development of our SmartParts solution. We’ve learned from our experience with the production of parts, that traceability, authentication and quality management have been real pain point for the adoption of additive for production applications. Most traditional quality management techniques and traceability methodologies don’t transfer well when you start applying them to additive manufacturing,” Burke said.
Some of the common issues Burke hears from customers include how to integrate 3D printing into a manufacturers existing quality management system and how to distinguish between parts from a variety of suppliers. There are a handful of MES systems from the likes of Authentise, Oqton/3D Systems, Link3D/Materialise, and 3YOURMIND. However, most apply their solutions purely from a software standpoint, perhaps using QR codes or part recognition and machine vision to manage parts. SmartParts does so within the actual material itself.
At the core of SmartParts is a programmable particle. The particle is made from undisclosed rare earth elements that, when subjected to pressure and heat in a controlled, proprietary manner, makes it possible to yield specific physical characteristics and optical responses. With this method, the PrintParts team can control the size, shape, and what Burke described as the “optical conversion” of the particles. This means that, when the particle is exposed to a wavelength on the light spectrum, it will return a given signal. For instance, a 940 nm infrared wavelength can be “programed” to return a 540 nm wavelength signal. This opens it up for a variety of applications, including part traceability.
“It’s similar to the way that an infrared remote works for a TV. When you hit the mute button, it sends out a specific infrared wavelength and your TV recognizes that and mutes itself,” Burke explained. “It’s similar to that, except that we’re actually programming a response back. And we use those levers to create an identification system.”
The company’s identification system consists of particle-powered taggants embedded into the printing material. The particles are incorporated into the base feedstock at parts per million levels, thus preventing any real contamination from impacting any material properties or print performance. Then, the finished components can be scanned with SmartParts scanning hardware, which reference the embedded material tag against a database of other IDs. This tag could be associated with information such as the part supplier, the lot in which it was manufactured, the material from which it was made and more. This allows for the necessary traceability to confirm that a component was made from a certified version of ULTEM, for instance.
A 3D printed part being scanned. Image courtesy of PrintParts.
While the ability to control optical properties is key for the SmartParts scanning system, controlling the size and shape of the programmable particles is necessary for suiting the material to a given feedstock.
“This is obviously very relevant for introducing it into a resin, for example, where you might need a very small size particle in a particular shape so that it won’t settle in the resin and will evenly suspend. If you’re introducing the particle into a powder, you have sets of characteristics around that shape and size so that it will spread and mix evenly into the powder,” Burke said.
Because modifying the particles is a step that takes place outside of the production of the part, this technology is quite flexible and could have myriad applications both in and outside of AM. For instance, the particles can be applied during post-processing, though incorporating them into the printing process is a more elegant solution. This opens up the possibility of treating parts with the particle, perhaps using some form of automated system from PostProcess Technologies, DyeMansion or Additive Manufacturing Technologies. However, it means that items made traditionally can be coated with SmartParts’ particles, as well. For this reason, such a solution could be valuable to multi-technology service bureaus like Xometry, Protolabs, FATHOM, and Siemens. If it has advantages behind current quality control methods, you could even imagine original equipment manufacturers like Ford or Airbus using it on conventionally made parts.
If you extend this line of thinking further, you might imagine it used beyond manufacturing altogether. With COVID vaccine passports explored and implemented by many governments and businesses, it’s easy to consider creating a digital passport that could be created upon vaccination. Programmable particles could be included in future versions of Moderna or Pfizer shot so that your vaccine passport is updated with the latest injection. PrintParts is currently focused on the AM industry and manufacturing, but it is likely that this technology will find its way to other industries.
A scanned 3D printed part matched against its data registry. Image courtesy of PrintParts.
Burke explained that the decision to focus on AM came from the fact that use of the technology in production environments is still immature. There has so far been a lack of standardization for quality control and traceability. Additionally, due to the the unique nature of AM, counterfeiting poses a unique problem.
“As the technology democratizes more and more, people have access to these printers and the issues associated with counterfeit parts are only going to increase. We think there’s a real opportunity to address that in additive. That being said, the systems that we’re building around the scanning technologies and software databases to store all of these digital records that we’re linking to the materials and to the parts are applicable for any manufacturing industry.”
He further explained how the company is executing a three-phased approach, which PrintParts has already begun, starting with working alongside additive OEMs and material companies to provide IDs for high requirement materials and parts. This will be followed by the introduction of the full SmartParts platform to manufacturers and users of parts to achieve full end-to-end traceability. Finally, SmartParts will expand to broader manufacturing technologies.
“We believe we can accomplish that in a number of ways with post-processing methods. We’ve experimented with adding the particle in dyes, coatings, and ionizing processes for a CNC metal part. So, we have a variety of delivery mechanisms that we can experiment with, but additive is a really nice early-stage market for us to attack,” Burke said.
The company aims to establish an ecosystem of partners who can benefit from the technology, tackling the entire value chain, from material compounders to end users. This includes materials companies, with whom PrintParts is conducting feasibility tests to determine if their particles can be added to materials for authentication, source of origin proof for environmental, social and governance reporting requirements, and for lot and batch traceability for different powders.
“Our goal here is to really enable an ecosystem of partners to gain value from this technology. We recognize that for our approach to work, we need to be technology agnostic and work with all of these players,” Burke said.
The startup is also looking into manufacturing execution system (MES) and enterprise resource planning (ERP) providers in the non-additive space about the possibility of linking up the SmartParts digital records platform to existing MES and ERP systems. About existing MES solutions for additive, Burke said the following:
“We’re getting the feedback from folks on the software side that traceability is a requirement to land these large deals with big auto and aerospace OEMs. MES providers have done an admirable job using the technology that’s available to introduce traceability. We can work together with those companies to add a higher level of fidelity.”
The company is currently developing a software integration program for MES developers to take the information they gather, such as digital twin and manufacturing data, and link it to SmartParts materials. Other opportunities exist in the automation space with companies like AM-Flow, which develops methods for conveying, identifying, and packaging 3D printed parts. With SmartParts, there’s the possibility of not just using machine vision to track a component based on its shape, but also within the material.
Given the current pace of growth in the market, it wouldn’t be surprising to this author that some of these flowering partnerships bloom into complete acquisitions. On the service bureau side, one could imagine a firm like Xometry or Protolabs purchasing PrintParts. For materials, the obvious contender would be BASF, which has inserted itself quite firmly into the service bureau market while also developing a wide variety of materials for 3D printing. As the largest chemical company in the world, it certainly has the money to begin introducing SmartParts programmable particles into its feedstocks. They could then be introduced to the world via BASF’s subsidiary Sculpteo and its spin-out spare parts business, Replique.
While it’s difficult to fully grasp how the SmartParts solution compares to existing methods for ensuring traceability in a production AM environment in terms of effectiveness and cost, it seems like a brilliant approach with huge potential from the outside. The product is only in beta testing at the moment, but we’ll get a better sense for use cases as they become public.
0 comments on SmartParts: Traceability in 3D Printing at the Particle Level – 3DPrint.com